Cutting and wiring standards for connection cable assemblies involve using established methods for preparing and connecting wires, adhering to industry best practices, and ensuring compliance with relevant codes and standards. Key aspects include proper wire stripping, termination techniques (crimping, soldering, usw.), and adherence to wiring schemes like T568A and T568B for network cables.
1. Cutting standards
Incision processing
When cutting the wire, it is strictly forbidden to damage the internal conductor (such as steel core), and the incision must be kept neat to avoid burrs or poor stranding of wire strands.
When stripping the insulation layer, special tools (such as wire strippers, electrician’s knife) should be used to avoid damaging the wire core; plastic hard wire is recommended to be cut at a 45-degree angle, and then push and peel.
Conductor exposure requirements
The wire core of the connection part should not have broken strands, missing strands or loose strands, and there should be no obvious loose strands near the pipe mouth after connection.
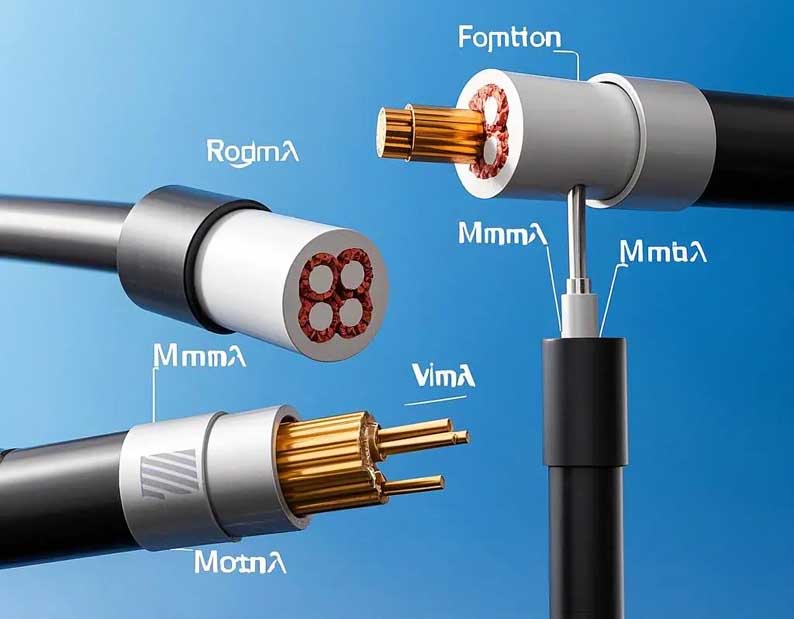
Cutting and Wiring Standards for Connection Cable Assembly
1. Wire Preparation and Cutting:
Stripping:
Remove insulation to expose the conductor for termination. Different stripping methods exist, including partial and full stripping, depending on the application.
Cutting:
Cut the cable to the desired length, ensuring the cut is clean and does not damage the conductors.
2. Wiring Schemes (e.g., T568A and T568B):
Twisted-Pair Cables:
For network cables, T568A and T568B wiring schemes specify the color order of the wires within the cable.
Consistency:
It’s crucial to use the same wiring scheme on both ends of the cable for proper connectivity.
3. Termination Techniques:
Crimping:
A common method for connecting wires to connectors, ensuring a secure and reliable connection.
Löten:
Used for certain applications, providing a strong and permanent connection.
Other Methods:
Other termination methods include insulation displacement connectors (IDCs) and wire wrapping.
4. Standards and Codes:
IPC/WHMA-A-620:
A widely recognized standard for cable and wire harness assemblies, providing criteria for acceptance and quality.
ANSI/TIA Low Voltage Cable Installation Standards:
Specifies requirements for low-voltage cable installations, including cable support and routing.
National Electrical Code (NEC):
Provides guidelines for electrical installations, including cable routing and protection.
OSHA:
The Occupational Safety and Health Administration provides regulations for workplace safety, including requirements for cable installation and protection.
Military Standards (MIL-SPEC):
Specific standards for cable assemblies used in military applications, emphasizing durability and reliability.
5. General Considerations:
Cable Support:
Cables should be properly supported to prevent damage and ensure long-term performance.
Cable Routing:
Cables should be routed in a manner that minimizes potential damage from physical contact or sharp edges.
Cable Protection:
Cables should be protected from environmental hazards like moisture, temperature extremes, and corrosive substances.
Connector Selection:
Connectors should be chosen based on the application’s requirements, including voltage, current, and signal type.
By following these standards and guidelines, it’s possible to ensure the quality, reliability, and safety of connection cable assemblies.
2. Wiring standards
Connection method
The wire core must be crimped or silver-copper welded, and direct binding is strictly prohibited; the joint resistance should not be greater than 1.1 times the resistance of the original wire core, and the tensile strength should not be less than 80% of the original wire core.
When branching, the branch line needs to be tightly wrapped around the main line for 6 Zu 8 turns (such as T-shaped connection), and ensure that the wire core is in close contact.
Cable type matching
Different types of cables (such as paper insulated cables and rubber sheathed cables) shall not be directly connected, and must be transitioned through junction boxes and connectors.
When the same type of cables are directly connected, rubber sheathed cables must use vulcanization hot patching or equivalent cold patching technology, and plastic cables must meet mechanical strength, sealing and other standards.
Shielding and grounding treatment
When connecting shielded cables, the shielding layer of the specified length must be stripped, and the shielding layer, armor layer and grounding core of all cables must maintain good electrical connection.
III. Tool and process requirements Special tool use
Special crimping pliers must be used for crimping operations to ensure that the crimping cap matches the wire diameter (such as T4 type crimping cap is suitable for 4 4mm² wires).
Fiber optic connections require the use of tools such as fiber pliers to avoid bending or stretching.
Wiring and protection
The cable bending radius must meet the specifications (such as ordinary cables ≥2 times the diameter, optical fibers ≥40mm), and avoid contact with sharp objects or extrusion by rotating parts during laying.
The connection parts need to be double wrapped with fireproof tape and insulating tape to prevent electric sparks or short circuits.
IV. Specifications for special scenarios
Communication cable connection
The all-plastic cable needs to be arranged according to the color spectrum (such as white/blue, red/orange, usw.), and the number of spare pairs should not exceed 1% of the nominal pair.
Modular connection needs to use non-hygroscopic cable ties to distinguish units and follow the clockwise arrangement rule.
Fiber optic cable connection
The cable with built-in optical fiber needs to fix the core through the connecting tube, and the optical fiber lead-out hole needs to be equipped with a protective component to avoid mechanical damage.
Note: The above standards need to be flexibly applied in combination with specific cable types (power/communication/optical fiber) and scenarios (such as high voltage, outdoor) to ensure safety and reliability.
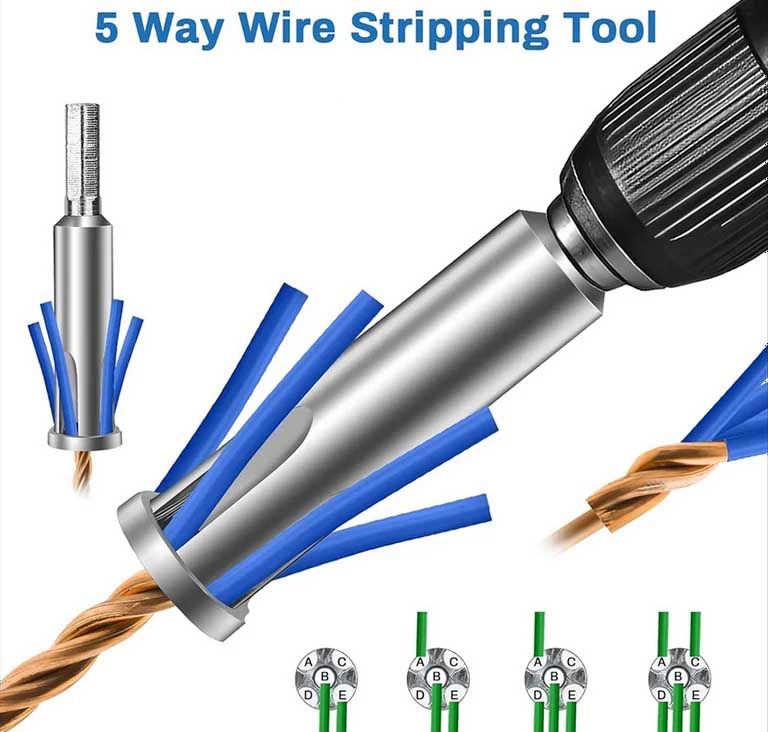
Universal Wire Twisting Tool, Wire Stripper and Twister, Quick Connector Twist Wire Tool