Key points of terminal harness assembly station design
Based on current technical specifications and industry practices, the design of terminal harness assembly stations needs to integrate factors such as structural adaptability, operational efficiency, safety and quality controllability. The following are key design directions and implementation suggestions:
1. Station structure design
Modular assembly unit
The station should be divided into independent modules such as terminal crimping, harness binding, sensor connection, etc., supporting parallel operations to improve efficiency.
Equipped with adjustable clamps and positioning devices to adapt to terminals of different packaging forms (such as epoxy resin, metal shell, etc.).
Drawing and parameter integration
Integrate CAD drawings and parameter annotation systems to display assembly steps and key dimensions in real time to reduce operational errors.
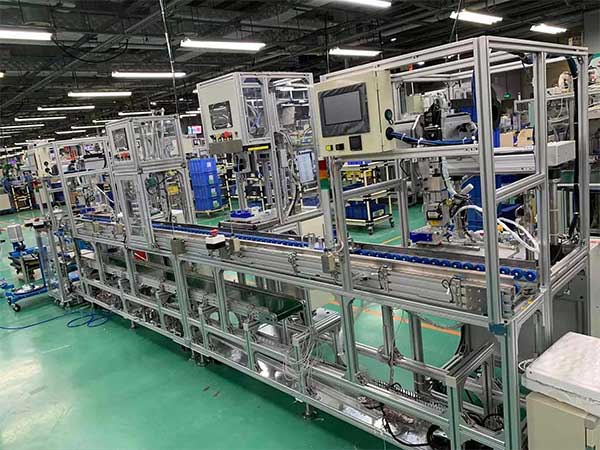
Fully automated terminal harness assembly station design
2. Tool and equipment configuration
Special tool selection
The crimping tool needs to match the terminal type (such as ring terminals, bullet terminals) to ensure uniform crimping force and no damage.
Equipped with high-precision wire strippers and heat shrink tube heating equipment to ensure the quality of cable insulation layer processing.
Automation equipment assistance
Introduce automatic wire feeding machines or robots to assist in threading to reduce manual operation intensity and improve consistency.
3. Operation process optimization
Error prevention and detection mechanism
Through color coding, polarity identification and photoelectric sensors, error prevention is achieved to avoid reverse wiring or missed connections.
Integrate a continuity tester or multimeter to detect harness resistance and connectivity in real time.
Environmental adaptability design
The workstation must have dust and anti-static functions, and be equipped with corrosion-resistant materials (such as fluoroplastic countertops) to adapt to medical or industrial environments.
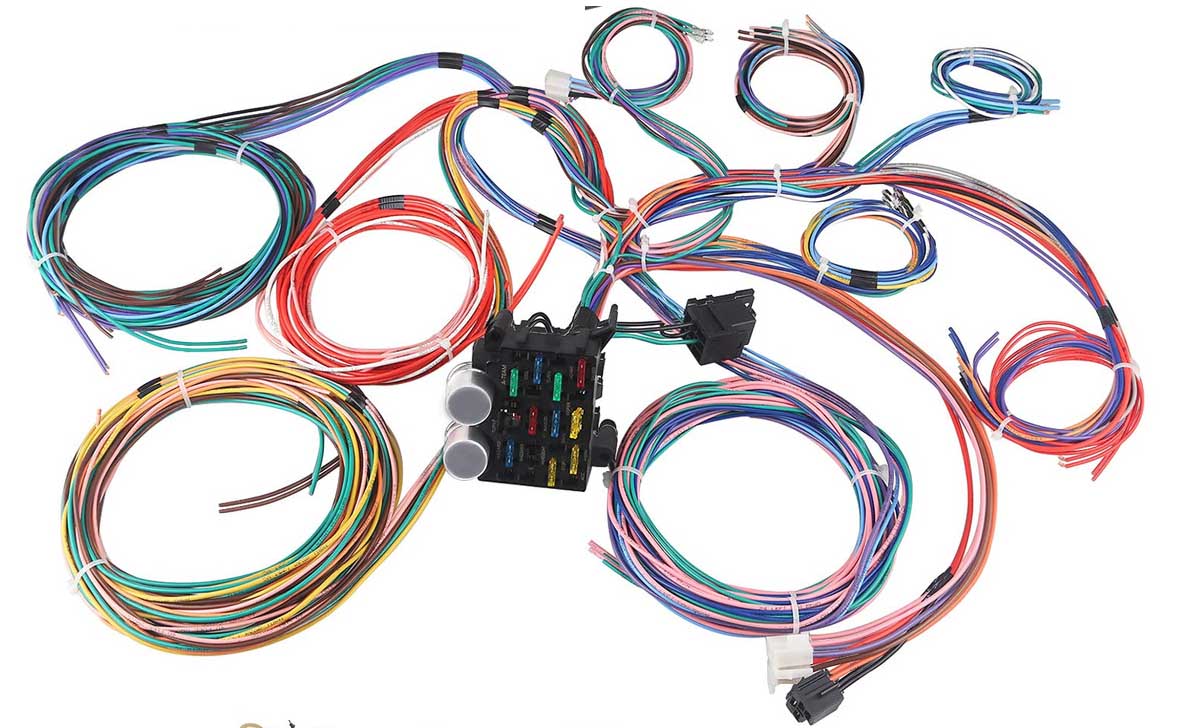
Rebel Wire 16 Circuit 12V Universal Wiring Harness China Made
4. Quality control and traceability
Calibration and verification links
After assembly, the sensor performance must be verified by a standard temperature source or simulated environment (such as NTC resistance drift ≤0.1%).
Record the test data of each batch of harnesses (such as temperature response time, accuracy deviation) to support quality traceability.
Ergonomic optimization
The workbench is height-adjustable and equipped with a magnifying glass or lighting equipment to reduce visual fatigue and improve operating comfort.
5. Adaptation of typical application scenarios
Wire harness assembly of medical equipment
It needs to meet the IP67 waterproof level, and use biocompatible materials to encapsulate the terminals to avoid the risk of human contact.
Energy storage system integration
In response to the temperature monitoring needs of the battery pack, a multi-channel wire harness layout is designed to support the rapid thermal management response of the BMS system.
Through the above design strategies, the terminal wire harness assembly station can achieve efficient and accurate large-scale production. Al mismo tiempo, it meets the stringent requirements of medical, industrial and new energy fields for reliability and environmental adaptability.
In the wire harness manufacturing process, the size and output of the wire harness are the key to determining different types of assembly processes.
Regardless of the type of wire harness, a pre-assembly station is required, and some wire harnesses also include blind plugging stations. For simple pre-assembly of the circuit, there is no need to make a pre-assembly board, just hold it in your hand for work. Pre-assembled complex plates can be produced to facilitate operation and self-inspection. This requires a detailed pre-installed work instruction so that employees can clearly understand the work content. Usually a pre-assembly instruction book should reflect the following contents:
① Position of the instruction book
② Wire number, color, wire diameter, hole position
③ Shell number, hole location and simple schematic diagram
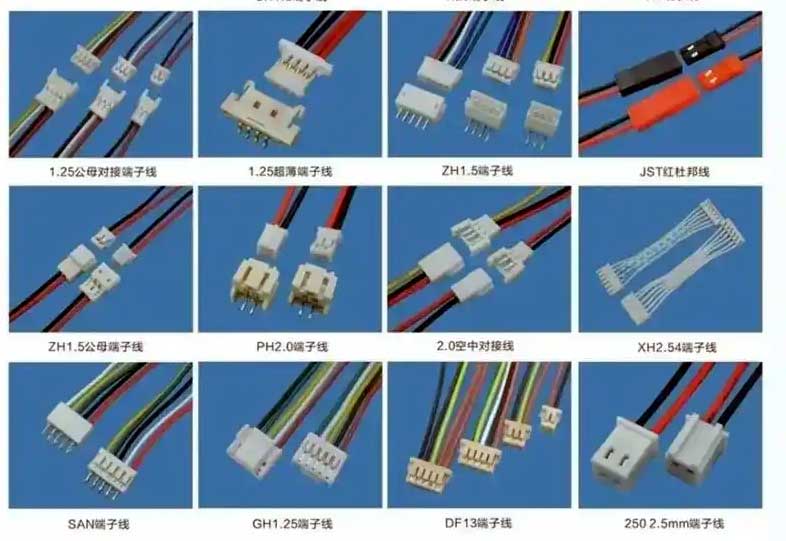
The Difference Between a Cable Assembly and Terminal Wire Harness
Process control points, that is, key points or precautions (including rubber parts, sensors, diodes, locking, etc.)
⑤ If encapsulation is required, the type and length of the tape should be reflected
⑥ Blind plug number and hole location
⑦ Auxiliary tool number
The instruction book uses the simplest and easiest-to-understand expression (such as visualization) so that employees can work quickly and less easily make mistakes. Before inserting the terminal, employees should check the terminal blade and appearance, and follow the principle of “one push, two listens, and three pulls”. When a “click” is heard, it means that the terminal is inserted in place. If the pre-assembled part of the housing is fully inserted, locks, covers or cable ties must be installed. The assembled housing pulls the wires back and the wires should not be pulled out. Each work station must conduct self-inspection after completion.
There are many pre-installed wires and materials, and the types are relatively complex. Their placement needs to follow a certain logical organization and not hinder the operator. The placement of parts should be consistent with the order of operations in the work instructions, from left to right and top to bottom. Conductors with the same color and diameter at the same station should avoid being adjacent and should be separated as far apart as possible. Each part must be labeled, showing photos, part numbers, limited quantities and other information. There must be at least 2 material boxes to ensure that normal operations will not be affected when resupplying, and there must be a location for empty material boxes to be evacuated. Special markings should be provided for special wires (such as gold-plated or airbags) to alert employees. Finalmente, after the pre-assembled branch is completed, it must be placed in a circle on the hanging pole or transfer trolley to facilitate the next step of the next station or final assembly.
From a broad perspective, the final assembly process can be roughly divided into three types: fixed plate, classic assembly line and “H”-shaped assembly line, and the special one is the flip plate.
For wire harnesses with few circuits and easy operation (such as car light wires, trunk wires, etc.), a fixing plate can be used. The number of boards can be increased or decreased according to the order volume, which is more flexible and convenient. As the number of circuits increases, when single boards cannot meet the output and production efficiency (such as engines, instrument panel lines, etc.), classic production methods such as dynamic assembly lines, 4-stations, and 8-stations are selected. But this is limited to the height of the board, and two operators are not allowed to perform parallel operations at the same time on one workstation. To solve this problem, the “H” shaped assembly line was created. This is especially suitable for wiring harnesses with complex circuits and many types of car models (such as body lines, interior cabins, etc.). The biggest disadvantage is that the rotation speed should not be too fast, as employees will suffer from motion sickness and will be tired when working with their heads down for a long time.
Pre-assembly and final assembly run through the entire wire harness assembly. Its production methods and division definitions are also particularly important, and also demonstrate the level of a process engineer. This is an endless road that requires continuous exploration and continuous improvement. I hope everyone can go further and further.