The following is a comprehensive guide to choosing cable ties:
I. Material selection
Nylon material: Generally suitable for environments between -40℃ and 85℃, with corrosion resistance, self-locking and insulation. For high-temperature areas such as the engine compartment, you need to choose nylon cable ties containing heat-resistant components (temperature resistance up to 105℃).
Engineering plastics: Such as Wintone Z63 material, with higher rigidity, low water absorption and chemical corrosion resistance, suitable for complex working conditions.
Stainless steel material: Suitable for scenes that need to resist higher temperatures (such as >105℃) or highly corrosive environments.
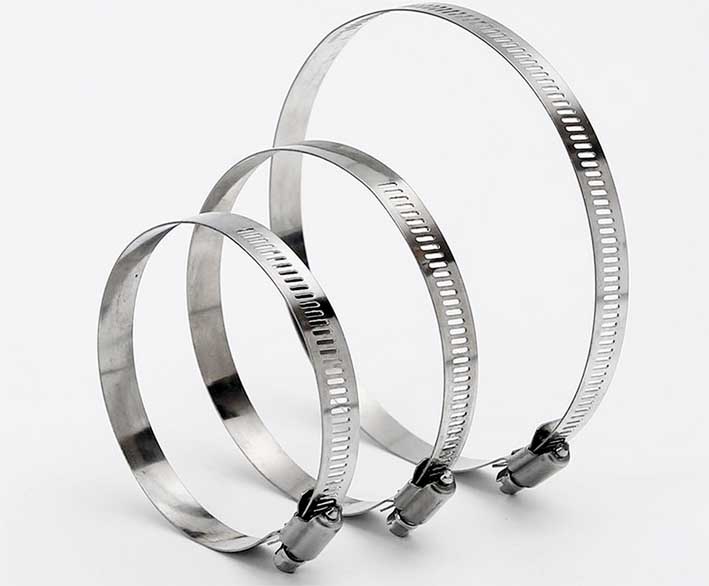
304 STAINLESS STEEL CABLE TIES STRON METAL TIE WRAPS ZIP TIE EXHAUST WIDE 10mm
UV-Resistant Nylon: Suitable for outdoor applications or areas exposed to sunlight.
Length and Width:
Measure the diameter of the bundle to be tied and select a tie that is long enough to wrap around the bundle with some extra length for threading through the locking mechanism.
Wider ties generally have higher tensile strength, making them suitable for heavier loads or larger bundles.
II. Specifications
Length and width
Single wire harness fixation: select 4×150 specification;
2-3 wire harnesses: select 8×175 specification;
Multiple wire harnesses: 8×240 specification is preferred, and 10×400 specification is used for temporary fixation when insufficient;
Spacing control
The chassis wiring harness fixing spacing is recommended to be 300-400mm to avoid sagging or driving sway;
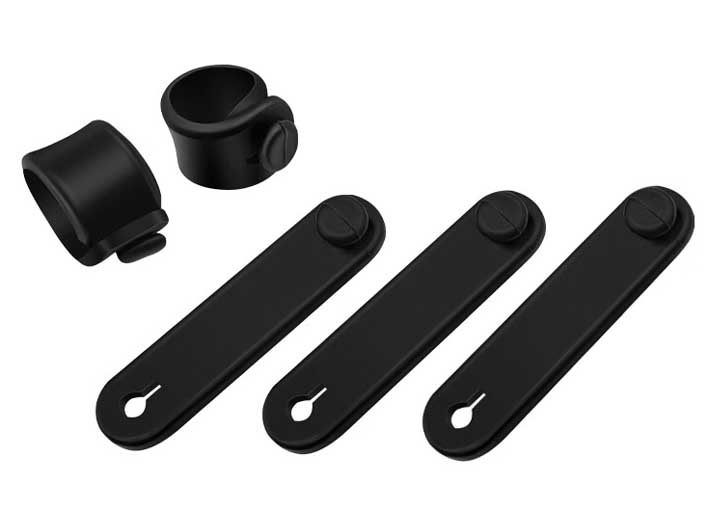
Rubber Band For Frame Securing Cable Ties Motorcycle Wiring Harness
III. Structural type
Fir-tree type cable tie: It is suitable for a wide range of plate thickness (0.8-3.5んん), but the pull-out force is low, suitable for areas with ample space;
Arrow-type cable tie: High pull-out force and compact size, suitable for plate thickness range of 1.5-2.5mm;
Welding stud type: Suitable for parts without openings on the body, and pre-welded studs are required for fixation;
Sheet metal card type: No opening design, but it is easy to scratch the sheet metal, and it is not recommended for the body;
IV. Tensile strength requirements
Minimum tensile strength: It must reach more than 2 times the weight of the harness, and ≥50% additional redundancy is recommended for vibration areas such as the engine compartment;
Locking mechanism: Preferentially choose a self-locking structure with a metal insert barb design to ensure that 2 teeth protrude after the locking teeth are engaged;
V. Installation requirements
The residual length after shearing is ≤3mm, and sharp burrs are avoided;
The direction of the cable tie head is as downward as possible to reduce the risk of loosening;
Special scenes (such as curved pipelines) require additional intermediate fixing points;
VI. Environmental adaptability
Ultraviolet protection: Choose black nylon cable ties containing UV stabilizers for outdoor scenes;
Chemical corrosion: It is recommended to use perfluoroalkoxy (PFA) cable ties in areas such as fuel lines;
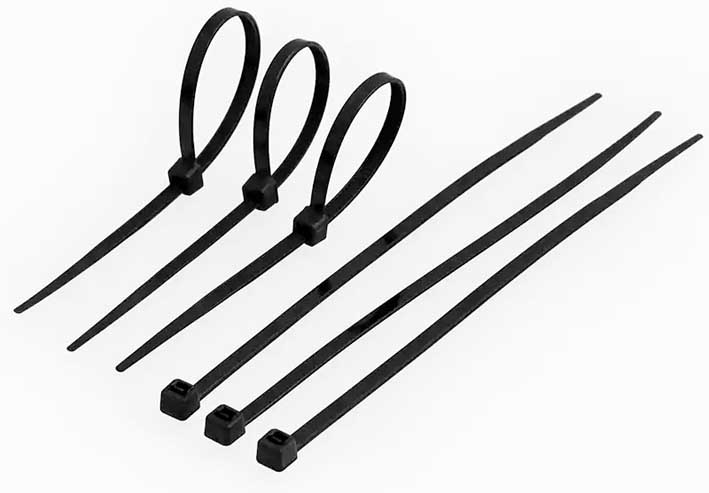
Custom Auto Car Automobile Wire Harness Tubing Fixing Buckle Self Locking Nylon Cable Tie
Tensile Strength:
The tensile strength of a cable tie is the amount of force it can withstand before breaking.
Choose a tie with a tensile strength that is appropriate for the weight and stress of the wiring harness.
Environmental Conditions:
Temperature: For high-temperature applications, select heat-resistant ties.
UV Exposure: For outdoor applications or areas exposed to sunlight, select UV-resistant ties.
Corrosion: For corrosive environments, choose stainless steel ties.
Other Considerations:
Reusability: Reusable ties are available for applications where repeated use is required.
Special Features: Consider ties with identification tags or other special features that may be needed for specific applications.
Installation:
Ensure the tie is properly installed and tightened to prevent slippage or failure.
Use a cable tie installation tool for efficient and consistent tightening.
Through the comprehensive consideration of the above dimensions, 安全性, economy and maintenance convenience can be balanced to achieve reliable fixation of the harness system.
With the increasing use of electrical and electronic components and subsystems, properly securing cables is an important aspect of system design that is often overlooked. Whether within equipment or between systems, ensuring that cables are routed safely, securely and efficiently is critical to the success and longevity of a design, especially in high-vibration and harsh-environment applications. This article’s wiring harness engineer mainly introduces how to select and apply the correct cable ties for wiring harnesses.
The challenge for designers is to find cable ties that meet application needs in terms of tensile strength, longevity, flexibility, chemical, vibration and ultraviolet (UV) radiation resistance. without over-engineering or compromising the integrity of the cable’s insulation and internal structure. This requires analyzing the many types of cable ties and various materials now available and differentiating them, fearing that choosing the wrong cable tie could end up costing much more than the purchase.
To alleviate these concerns, designers need to understand the nuances of cable ties and how to align their selection with application requirements. This article will outline the considerations for cable ties, the advantages of each type, and how to apply them effectively using real-life examples from Panduit Corporation.
Tie specifications
Cable ties, often called zip-ties or tie wraps, are available in a variety of lengths, widths, materials, and colors. When bundling a wire bundle, the tie or tape portion should be wrapped around the wire bundle, pulling the loose end completely through the locking mechanism and tightening until the strap locking notch is securely engaged (形 1).
形 1: A typical cable tie showing the main components used to secure a cable bundle.
The cable tie may be constructed as a single piece with the locking barbs molded as part of the locking mechanism. In contrast, higher quality ties have a two-piece construction. In the two-piece design, corrosion-resistant stainless steel barbs are embedded into the lock head to grip the relatively smooth lacing surface. It is designed to provide a secure lock that is infinitely adjustable, as the barbs do not need to fit into the locking grooves.
The maximum diameter specification indicates the largest diameter wire bundle that the tie can accommodate. The bundling should be securely fastened without over-tightening and cutting or abrading the cable insulation. The length of tie used should allow for an extra point to engage the loose end in the locking mechanism.
The strength of a wrap is defined as the loop tensile strength (LTS) measured in pounds. LTS is the maximum force that can be exerted when the locking mechanism is engaged. The most common ties are between 18 pounds and 250 pounds.
LTS depends on the size of the tie and the material used. Material selection is primarily influenced by the environmental operating conditions the tie will experience. Considerations include:
Is it for internal or external use?
What is the expected temperature range?
Will it be exposed to water, oil, chemicals or vibration?
例えば, Panduit’s PLT1.5M-M10 cable ties are part of the company’s PAN-TY@PLT series of ties. This line of cable ties is its largest and most comprehensive range, offering ties in a variety of colors, materials and construction types. The PLT1.M-M10 has a nominal length of 5.6 inches (inches), a rated maximum diameter of 1.25 inches, and a tensile strength of 18 pounds. Frenulas are classified by their cross-sectional area as extra-small, micro, or intermediate. The PLT1.M-M10 is a miniature tie with a one-piece construction design. It is made of nylon 6.6 and is suitable for indoor use.
As mentioned earlier, another common cable tie design consists of two pieces with a separate stainless steel barb that replaces the molded nylon barb in the one-piece design (形 2).
形 2: Single-piece fabrication with molded locking barbs (a) shown along with two-piece fabrication (b) using stainless steel barbs inserted after forming.
The aqua cable tie shown on the left in Figure 2 is one of the variants of Panduit’s PLT3S-C76 — PAN-TY@PLT series. It is made from ethylene tetrafluoroethylene (ETFE) and is suitable for applications requiring chemical resistance, flame retardancy and radiation resistance. The cable tie on the right in Figure 2 is Panduit’s BT4S-M0, a member of the DOME-TOP BARB-TY BT series, manufactured with individual barbs. Additionally, this series of ties features rounded heads and rounded edges to minimize wear on the wire insulation. The black color is achieved by adding carbon black to the nylon, which improves resistance to UV rays, making this color more commonly used in outdoor applications.
Cable ties are manufactured from a range of materials specific to the environment in which they are intended to be used. The basic lacing is molded from nylon 6.6. Nylon 6.6 offers high mechanical strength, stiffness, good heat resistance and reasonable chemical resistance. Variants include weather-resistant, heat-stable and flame-retardant nylon 6.6.
Various other materials are used to achieve specific tolerances. 例えば, the DT8EH-Q0 is designed for high strength as well as resistance to impact, chemicals, UV rays and weather. It uses acetal (polyoxymethylene, or POM), a range of materials including Delrin. It is 2.25 足 (ft.) long and has a tensile strength of 250 pounds. These cable ties are designed for harsh outdoor applications in the power and communications industries.
temperature range
The temperature range that a cable tie can withstand depends primarily on the materials used in its construction. Nylon 6.6 is rated for an operating temperature range of -76°F to +185°F. Heat-stable nylon 6.6 extends the upper end of the range to 212°F. PEEK has the highest temperature tolerance, with an upper temperature limit of 500°F.
special function
The Panduit CBR1M-M, part of the Contour-Ty Series, features a unique design that prevents damage to wire insulation or cable jacketing. It features a low-profile head design that uses parallel inlets to limit exposure of sharp edges and reduce snags, and features locking indentations on the outside of the strap (形 3).
形 3: The Contour-Ty Series uses a locking mechanism that is set at right angles to the strap section for parallel insertion and locks notches on the outside to prevent damage to the insulation.
HV9150-C0 push-in cable ties are made from weather-resistant nylon 6.6. Mechanically, it adopts a double-wedge design locking mechanism to achieve fixed locking and flexible locking (形 4).
形 4: The HV9150-C0 features an in-line design that allows parallel access to the locking mechanism to reduce the height of the cable bundle.
The releasable head allows for temporary binding before final locking. Indentations are molded into both sides of the strap, providing extra locking strength and greater flexibility. It has a length of 1.721 足, a beam diameter of 5.92 inches, and a tensile strength of 160 pounds.
SST1.51-M cable ties are 5.3 inches long and have a tensile strength of 40 pounds (形 5). It is designed with a small head height for general bundling and through-panel applications. Its two-piece design has what Panduit claims is the lowest stringing force in the industry and is 14% lighter than a one-piece design. Additionally, the straps are releasable before final tightening.
形 5: The SST1.51-M two-piece design uses a floating ring to lock the strap to a toothed wedge. The ties can be loosened by pulling the collar back and bending the wedge away from the straps before final locking.
Where most cable ties have low stretch capabilities, the body of the Panduit ERT2M-C20 is designed to be flexible (形 6).
形 6: ERT2M-C20 elastic cable ties feature flexible straps that prevent over-tightening.
This type of zip tie is designed to conform to a bundle of wires or fiber optic cables to prevent over-tightening. It also has a high coefficient of friction that grips wires to prevent lateral movement. This removable cable tie is 8.5 inches long and has a tensile strength of 18 pounds. Like other ties in the range, it has a UL94V-0 flame retardant rating – meeting strict telecommunications flammability requirements – and is halogen-free and non-toxic.
The SG100M-M0 is suitable for use in maintenance, repair and overhaul environments as well as rough installation practices in the construction industry (形 7).
形 7: The SGM100M-M0 cable tie features a low mounting head height, flared neck, and tapered tip for easy threading.
It’s made from weather-resistant nylon 6.6, making it ideal for applications subject to intense UV exposure. It is 4.2 inches long and has a tensile strength rating of 18 pounds. Its thin, wide straps are designed to flexibly grip cable bundles and reduce lateral wire movement.
in conclusion
Although cable ties are often considered relatively simple, designers need to carefully consider the many available options to ensure the most appropriate tie is used for the application. As shown, cable ties are available in lengths from inches to several feet, are compatible with a variety of environments, and have many features to meet the needs of a variety of applications.