The reliability of power and signal cables directly affects the stability and life of electronic equipment. Its analysis needs to be carried out from multiple dimensions such as materials, design, environmental adaptability, and signal integrity. The following are key analysis points:
1. Material and structural design
Conductor and insulation material selection
Conductors need to use high conductivity and corrosion-resistant materials (such as copper alloys), and pay attention to the relationship between current carrying capacity and temperature rise to avoid aging caused by overload.
Insulation materials must meet the requirements of high temperature resistance, flame retardancy and chemical corrosion resistance, such as silicone or polytetrafluoroethylene (PTFE).
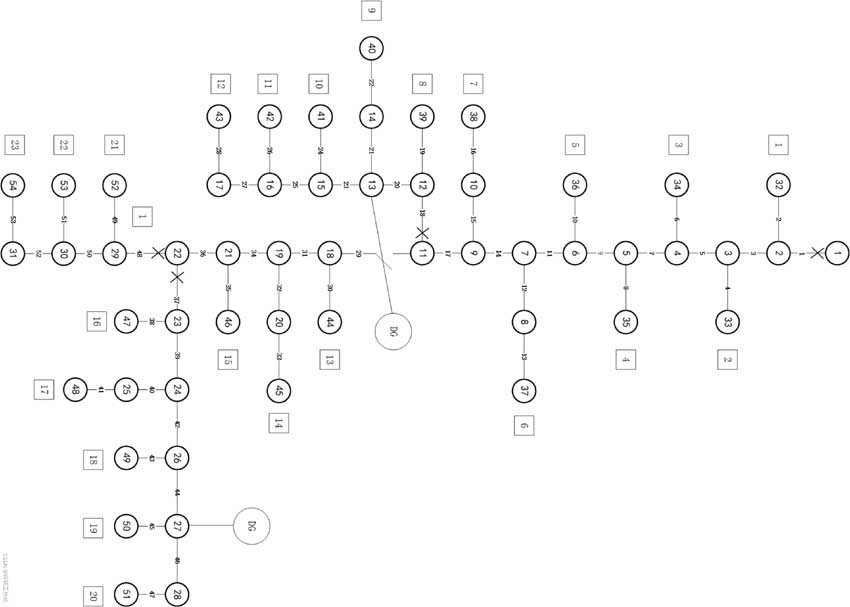
Reliability Analysis of power & Signal Connecting Cables
Mechanical structure design
The plug-in life needs to be improved through locking structure optimization (such as snap-on connectors) to improve vibration and impact resistance.
Redundant design (such as twisted pair or dual power supply) can reduce the risk of single point failure.
2. Environmental adaptability
Temperature and humidity influence
High temperature environment may accelerate the aging of insulation materials, and low temperature may easily cause conductor embrittlement, and performance needs to be verified through high and low temperature cycle tests.
In high humidity environments, the protection level (such as IP67) needs to be improved by moisture-proof coating or sealing structure.
Environmental Factors:
Analysis considers the influence of factors like temperature, shock, vibration, and humidity on cable performance.
Material Properties:
The choice of materials for conductors, insulators, and sheathing significantly impacts cable reliability.
Manufacturing Processes:
Quality control and adherence to manufacturing standards are crucial for ensuring reliable cable construction.
Test and Simulation:
Various tests, including life testing, environmental chamber testing, and numerical simulations, are employed to evaluate cable performance and predict potential failures.
Fault Localization:
For power cables, fault localization is a critical aspect, especially in high-voltage systems where single-core cables can be more challenging to diagnose.
Data-Driven Methods:
Analyzing historical failure data can help identify patterns, predict future failures, and inform maintenance strategies.
Electromigration:
In integrated circuits, electromigration (EM) analysis is vital to ensure the integrity of interconnects over time.
Separation of Power and Data Cables:
In some cases, maintaining a certain distance between power and data cables is essential to minimize interference, especially in networking applications.
Why Reliability Matters:
Stable Signal Transmission:
Reliable connectors ensure stable signal transmission, crucial for various applications.
Reliable Power Supply:
Reliable power cables are essential for preventing power outages and ensuring the safe and efficient operation of systems.
Reduced Costs:
Reliability analysis can help identify and mitigate potential failure points, leading to reduced maintenance costs and downtime.
Safety:
Reliable cables are critical for safety, especially in applications involving high-voltage power systems.
By understanding these aspects, engineers and manufacturers can design, manufacture, and maintain power and signal connecting cables with the highest reliability possible.
Vibration and mechanical stress
Dynamic vibration testing needs to simulate actual working conditions to ensure that the contact resistance of the connector is stable under vibration conditions.
III. Signal integrity analysis
Electromagnetic interference (EMI) protection
Shielding design (such as metal braid or twisted pair) can reduce the interference of external electromagnetic fields on the signal 38.
Grounding design needs to avoid common ground loop noise and adopt star grounding or independent grounding strategy .
Impedance matching and noise suppression
The signal line needs to maintain consistent characteristic impedance, and use termination resistors or filter capacitors to suppress high-frequency noise .
IV. Reliability test verification
Static test
Measure the insulation impedance when not powered on (such as the power line to ground impedance) and the static voltage stability after power on .
Dynamic test
Dynamic load test: Monitor voltage fluctuations and ripples under different loads (no load, full load) (the oscilloscope bandwidth is limited to 20MHz) . Power supply noise test: Use grounding springs to ground nearby to reduce spatial coupling noise interference.
Life and durability test
Repeated plug-in and pull-out tests verify mechanical life, and power-on and power-off cycle tests evaluate long-term stability.
MTBF (mean time between failures) calculations require the combination of component failure rate and environmental stress data.
V. Typical failure modes and protective measures
Poor contact
Cause: oxidation, mechanical wear or loose connection.
Measures: gold-plated/silver-plated contacts, additional locking mechanism.
Insulation aging and breakdown
Cause: material degradation or overvoltage shock.
Measures: derating design (such as voltage margin ≥ 20%).
Signal distortion caused by electromagnetic interference
Cause: unshielded or poor grounding.
Measures: optimize wiring spacing and increase magnetic ring filtering.
VI. Summary
Improving the reliability of connecting wires requires comprehensive material selection, redundant design, environmental testing and EMC optimization, and verifying performance through strict static/dynamic tests. Key indicators include contact resistance stability, insulation withstand voltage strength and temperature rise control under long-term load.
Reliability is an emerging scientific discipline in recent years, which always runs through all technical fields. The safety of automotive wiring harness design is crucial to the entire automotive electronic system. The reliability of the wiring harness design is a reflection of safety. This article’s wiring harness engineer’s automotive wiring harness reliability analysis content.
Reliability analysis of line terminals and connectors
As an important part of the automotive wiring harness, line terminals and connectors are the main components that determine the reliability of the wiring harness system and play a vital role in the wiring system. Terminals and connectors account for a large part of the many problems that occur in wiring harnesses. 예를 들어, the terminals are aging, and the connector components have fallen off, loosened, and been damaged due to time. These problems may be a small detail in normal times, but if placed in the entire wiring harness safety system, they will lead to a reduction in the safety and reliability of the wiring harness. Therefore, in the usual wire harness design, certain measures must be taken to ensure the reliability of the wire harness design. 예를 들어, during the installation process, choose appropriate connectors and plug-ins, 등.; secondly, pay attention to their materials. The operating temperature of terminals and connectors and the maximum allowable current; pay attention to their working environment and temperature. At the same time, it is necessary to avoid some corrosive gases or liquids from affecting the terminals and connectors, thereby destroying the reliability of the entire electronic system.2 Analysis of the reliability of wire harness protection
The working environment of automobile wiring harness is very harsh, often accompanied by corrosive gases and liquids, as well as high temperature, humidity, and collision and friction with other parts. Problems such as damage to the insulator jacket and loose interfaces often occur, resulting in short circuits or open circuits in the wiring harness, affecting the overall electronic system. Therefore, in order to improve the safety of automobile wiring harness design, it is necessary to make a work plan for wiring harness design and effectively wrap and fix the wiring harness. The design of automobile wiring harness should have measures such as moisture-proof, anti-corrosion and anti-high temperature. At the same time, it is necessary to ensure that it has good air-tight materials to protect the joints and connectors. When installing wiring harnesses in other parts of the car body, professional cable ties and wire clips should be used to fix them to reduce the impact of vibration on the car’s wiring harness during driving. At the same time, some connection positions must be protected to avoid friction between the wire control and the wiring harness, which will lead to wear and tear of the insulating coat. When packaging, it is necessary to analyze the different operating environments of different components to characterize their service life and reliability. It is necessary to conduct various comparative tests on materials to select appropriate materials. It is also necessary to conduct experiments on the reliability of wiring harnesses in harsh environments to prevent substandard products from flowing into the next step.3. Reliability analysis of circuit design of wiring harness
The design of automobile wiring harness system is a very complex project, especially the current loop problem of the line. Under certain environmental conditions, the rational design of the circuit is the core of the electrical system. Under normal circumstances, the circuit line system of a car is connected in parallel among different electronic devices. To test its lines, it is necessary to change the connection method of the lines and simulate what may happen under various circumstances to ensure the normal operation of the wiring harness line system.